Porosity in Welding: Identifying Common Issues and Implementing Finest Practices for Avoidance
Porosity in welding is a prevalent concern that frequently goes unnoticed until it triggers considerable troubles with the honesty of welds. In this conversation, we will check out the vital variables adding to porosity development, examine its damaging impacts on weld performance, and discuss the finest practices that can be taken on to minimize porosity event in welding processes.
Common Sources Of Porosity

Utilizing dirty or wet filler products can present pollutants right into the weld, contributing to porosity issues. To mitigate these common reasons of porosity, detailed cleaning of base steels, correct shielding gas selection, and adherence to optimal welding parameters are crucial practices in attaining top quality, porosity-free welds.
Effect of Porosity on Weld Top Quality

The existence of porosity in welding can substantially jeopardize the architectural integrity and mechanical buildings of welded joints. Porosity creates spaces within the weld steel, weakening its total strength and load-bearing ability. These voids function as stress and anxiety focus points, making the weld much more prone to cracking and failing under used loads. Additionally, porosity can lower the weld's resistance to deterioration and other ecological variables, additionally decreasing its durability and efficiency.
Among the main effects of porosity is a decrease in the weld's ductility and toughness. Welds with high porosity degrees tend to show lower effect toughness and decreased capability to flaw plastically prior to fracturing. This can be particularly worrying in applications where the welded parts are subjected to dynamic or cyclic loading problems. Porosity can impede the weld's ability to efficiently transfer forces, leading see this to premature weld failing and possible safety dangers in essential structures. What is Porosity.
Ideal Practices for Porosity Avoidance
To boost the architectural stability and quality of bonded joints, what particular actions can be implemented to minimize the event of porosity during the welding process? Utilizing the right welding strategy for the certain material being welded, such as changing the welding angle and weapon placement, can further avoid porosity. Regular examination of welds and instant remediation of any type of issues identified during the welding process are vital practices to avoid porosity and create top quality welds.
Importance of Proper Welding Techniques
Executing appropriate welding Get More Information methods is vital in making certain the architectural integrity and quality of welded joints, building on the foundation of reliable porosity prevention procedures. Welding strategies directly impact the overall stamina and toughness of the welded framework. One crucial aspect of correct welding strategies is preserving the correct warmth input. Extreme warm can lead to raised porosity because of original site the entrapment of gases in the weld pool. On the other hand, insufficient warmth may cause insufficient blend, developing potential powerlessness in the joint. Additionally, utilizing the ideal welding criteria, such as voltage, current, and take a trip rate, is vital for attaining sound welds with marginal porosity.
In addition, the option of welding process, whether it be MIG, TIG, or stick welding, need to align with the particular requirements of the project to guarantee optimal results. Appropriate cleaning and preparation of the base steel, as well as selecting the appropriate filler product, are also vital parts of skilled welding strategies. By sticking to these finest methods, welders can lessen the danger of porosity formation and create top notch, structurally sound welds.
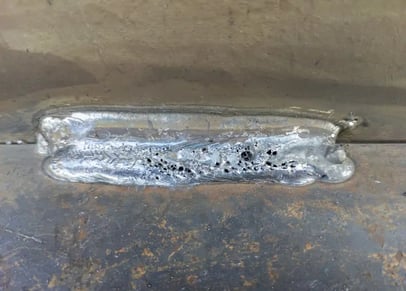
Examining and Top Quality Control Actions
Testing procedures are crucial to spot and protect against porosity in welding, ensuring the toughness and toughness of the last item. Non-destructive screening techniques such as ultrasonic screening, radiographic testing, and aesthetic assessment are frequently employed to determine possible issues like porosity.
Post-weld examinations, on the various other hand, analyze the final weld for any kind of flaws, consisting of porosity, and verify that it satisfies defined criteria. Applying an extensive high quality control strategy that includes complete testing procedures and inspections is critical to minimizing porosity concerns and making sure the overall quality of welded joints.
Conclusion
To conclude, porosity in welding can be a common concern that impacts the high quality of welds. By recognizing the typical root causes of porosity and carrying out best techniques for avoidance, such as proper welding strategies and testing measures, welders can guarantee excellent quality and trusted welds. It is necessary to prioritize avoidance approaches to minimize the occurrence of porosity and preserve the stability of welded structures.
Comments on “What is Porosity in Welding: Common Resources and Reliable Solutions”